In a company, one must undoubtedly pay attention when it comes to quality. Not only the final product or service – the one that reaches the customer directly – needs to be of quality, but all the processes leading up to it.
Why? Because it is precisely this care along the way that will provide truly effective delivery. But what lies behind quality management and how do we have parameters to know if we are on the right track?
To address this important topic, we have prepared this article. Here, you will deeply understand what the 7 principles of quality management are and how to apply them in your business starting now.
Keep reading to find out more!
What is Quality Management
Before discussing the principles, it is interesting to address the concept of quality management, which can be defined as the coordination of all actions that integrate productive and operational processes to be performed with quality.
Managing this has the objective of seeking excellence in task execution, taking into account factors such as performance, reliability, durability, compliance, and service.
Quality management is one of the stages of the entire quality process within an organization, being the link between quality control and assurance. Thus, it involves the analysis of data collected in inspections, non-conformities, action plans, and audits.
With the study of data, it is possible to have a more realistic and complete view of the company when it comes to quality. From this, senior management can work better to make processes increasingly accurate in delivering the product to the customer and maintaining the company’s competitiveness in the market.
What are the Quality Principles
It is not possible to talk about quality management principles without mentioning ISO 9001, as this is the standard where they are present. Its purpose is to offer a set of requirements in a standard and common order for the Quality Management System (QMS), which allows interaction with other management systems.
Following the guidelines provided by certification undoubtedly brings benefits to companies that want to gain prominence and relevance in the market and also achieve better results in various aspects.
The 7 quality principles are the foundation of ISO 9001:2015, so it is essential to know what they are and their requirements, as they should guide your business’s quality management system, being practiced by employees, especially those in leadership positions.
What are the 7 Quality Management Principles
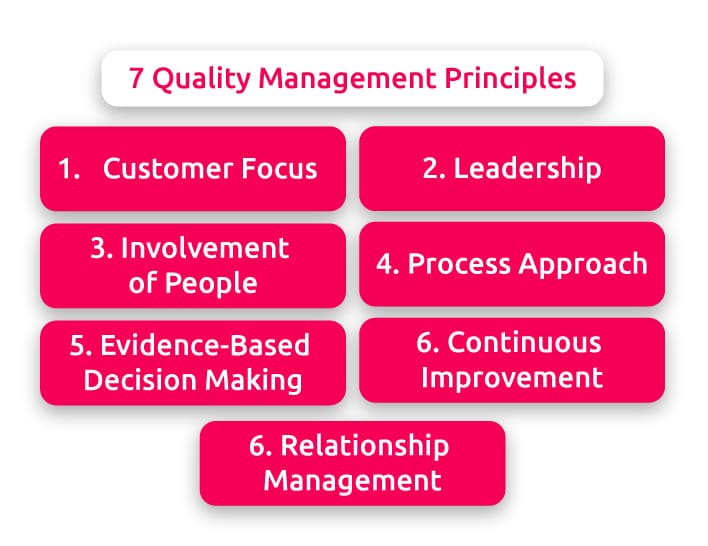
Now is the time to know what the 7 quality management principles are that every company needs to know if it wants to grow sustainably and strategically. Below, check what they are and what each one encompasses:
Principle 1: Customer Focus
The first principle of quality management is customer focus. After all, every quality management system aims to have satisfied customers – both external and internal, which consequently results in more sales and better overall results. For this, it is necessary to always keep in mind that the customer is the focus during the execution of processes.
After all, there is no company without customers, regardless of whether they are consumers of products or services. It may seem strange, but sometimes we can forget that the customer is indeed the main pillar for an organization to stay afloat. So, all attention is essential at this point.
A company that wants to grow should, in addition to meeting current customer demands, look ahead and also anticipate future ones. With this, customer expectations are not only met but exceeded, which contributes to loyalty.
When we talk about this first principle, it is necessary to consider that every opportunity for interaction with the customer is an opportunity to create more value and trust. Other benefits of maintaining a focus on the customer include achieving an excellent reputation, building an expanded customer base, and, of course, increased revenue and market share.
To maintain customer focus, companies must adopt and maintain actions that allow, for example, linking the organization’s objectives to customer needs and expectations, communicating them throughout the organization (so everyone works towards the same goal). Also, it is necessary to constantly monitor customer satisfaction.
One thing is certain: the more processes seek customer satisfaction, the higher the quality of the products and services that will reach them.
Principle 2: Leadership
The second principle of quality management is leadership. Today, there is already more awareness that leadership goes far beyond a position where the main functions are to command and indicate what should be done.
Being a leader is primarily about inspiring employees to work towards a common collective goal. In addition, it is necessary to bear in mind that, at some point, the team may continue with a new leader, but the quality standard must be maintained.
It is worth noting that the influence of effective leadership is enormous since it can guide employees to do their best in their tasks, performing each process correctly, whether it is change, specific actions, or results.
Innovative companies that invest in quality management certainly have good leaders at their forefront. The leader should be a proactive figure and the first to defend and follow the business purpose, acting authentically and thus becoming an example.
With leadership that integrates and directs employees, engagement is established naturally and allows everyone to remain aligned with strategies in pursuit of objectives, including those related to quality.
The advantages of having effective leadership include better coordination of processes, clearer communication between different levels and teams, and more assertiveness in pursuing desired results.
To invest in leadership, it is necessary to define and maintain unquestionable values, develop and nurture a culture of trust, offer training for improvement, as well as inspire, encourage, and recognize people for their contributions to the company.
Principle 3: Involvement of People
The third principle of quality management is the involvement of people. At this point, it is always good to remember that a company is made up of people, and they are responsible for making the delivery of the product or service to the customer possible.
Thus, it is important to understand that employees’ skills are the way for the business to be maintained and, more than that, to always seek innovation. After all, a company’s greatest asset is its human capital. Therefore, it is necessary to identify the positive points and develop each employee’s strengths, in order to enhance what they do best and mitigate and develop what may bring difficulties.
There is no doubt that each person has a particular potential, which must be used to solve problems and bottlenecks that are hindering the achievement of maximum quality. With real involvement of people, at all levels of the company, it becomes easier to create value for customers, as they will be in possession of their own power.
At this point, it is worth highlighting the importance of respecting differences, as well as valuing the contribution of each one, in the sense that every function is important for the whole to function correctly, like a gear. Gratitude also motivates employees, as they feel seen and recognized.
Among the gains for the organization that invests in people involvement are greater commitment to actions that include personal development, improvements, and creativity, an environment with more trust and collaboration, and the practice with more emphasis on values in the organizational culture.
To increase engagement, some actions to take are; have clear communication about the importance of each one, offer channels and tools for debates and knowledge sharing, give authority for decision-making, carry out performance evaluations, and listen to opinions.
Principle 4: Process Approach
The fourth principle of quality management is the process approach. In this regard, standardization is an important factor. For it to become a reality, it is necessary, first of all, to create processes and then look at the execution of each one to maintain quality.
For the process approach to yield results, it is essential that each employee is willing to perform their functions following the same standard and with maximum excellence. Thus, it can be determined whether the processes are effective or need to be changed.
When we talk about this principle, it is important to emphasize that all processes in an organization “communicate” with each other, which means that one impacts the other. Processes must be identified, understood, and managed so that they build the entire system of the company.
Each process is also a tool for communication with other areas of the organization. There are, for example, different processes that directly involve the customer, suppliers, or the employees themselves. All must work together to maintain quality.
In other words, having a comprehensive view of processes operating together increases the chance of achieving the goals established by the company. The principle of systemic management approach, therefore, seeks to bring clarity about the connection of one process to another and thus perceive what is not flowing yet and causing losses.
It is important that everyone in the company is aware of how the processes relate and the importance of maintaining harmony. Thus, those responsible for the processes and their employees perceive the impact they have on others, as well as the impact they receive, providing an opportunity to make operations even more effective.
Some of the benefits of a process approach include bringing opportunities for improvement and consistent results through a standardized system, process optimization, efficient use of resources, reduction of bottlenecks, and greater credibility of the organization in front of the audiences with whom it interacts.
To put this principle into practice, it is important, among other points, to monitor processes, delegate authority and responsibility, promote performance analysis, and manage risks that can affect processes and the quality management system itself.
Principle 5: Evidence-Based Decision Making
The fifth principle of quality management is evidence-based decision making. It involves monitoring and evaluating the processes mentioned above. With the exercise of analysis, based on accurate information, it is possible to access real data that allows identifying flaws in execution.
Like a living organism, every company has flaws. It is natural, especially when dealing with a large organization. However, this principle is precisely to identify and work on correcting errors accurately. Thus, resources of all types are saved.
On the other hand, the information collected is also a means to optimize processes by implementing improvements, making already good results even better.
However, we know that decision-making is not such a simple task. Therefore, it is important to reinforce that it is necessary to have reliable data at hand, as the quality of available data directly impacts the security of decisions.
Undoubtedly, the organization that combines logical and intuitive analyzes, the best of both worlds, has a greater chance of deciding correctly, which means leaving aside impulsiveness, acting based on precise data and common sense.
Thus, achieving goals in relation to quality depends on the company’s ability not only to monitor but mainly to analyze real data and facts and make decisions. It is also necessary to accept that uncertainty comes along and that there is no guarantee of 100% accuracy.
Decisions based on evidence bring benefits such as constant accurate and safe decision-making, improved management effectiveness, enhanced performance evaluation, and greater ability to achieve goals.
What can be done to apply this principle is to establish, measure, and monitor indicators, provide important data to strategic people, use appropriate methods to analyze information, and ensure the necessary competencies for data evaluation.
Principle 6: Continuous Improvement
The sixth principle of quality management is continuous improvement. It should be applied after the implementation of the aforementioned principles. Also, as the name suggests, it should be in constant action. The question to ask here is: what can be improved? After all, there is always something that can be improved, at some point.
Just as we are always seeking to grow, processes must also evolve. Customer demands are another important factor because they can undergo transformations. So, if the organization wants a satisfied customer, it cannot fail to regularly question what else can be improved.
Some examples of improvements that should be monitored frequently are customer service, manager performance, and employee performance. However, we know that there are several other important examples to follow in order to continue growing and gaining prominence in a market as competitive as the current one.
It is easy to see that companies that focus on always improving are the most successful because seeking improvements is directly connected to the business’s ability to react to changes. Thus, in a crisis, for example, it can see opportunities more easily and remain competitive.
The benefits of maintaining continuous improvement are numerous, such as greater customer satisfaction, more effective processes, better ability to react to risks and opportunities, and stimulation of innovation, which is so necessary.
For improvements to be continuous, it is interesting to set improvement objectives and goals at all levels of the company, monitor planning, implementation, completion, and results, and also recognize and communicate what has been achieved.
Principle 7: Relationship Management
The seventh principle of quality management is relationship management. As we know, relationships are a very important variable for any business. It occurs between the company and the customer, the company and suppliers, the company and employees, the company and investors, the company and society, among other parties.
When we talk about the organization and the customer, it is essential to have and maintain open communication channels. It is through clear and transparent communication that details, misunderstandings, and even possible improvements can be seen.
Regarding contact with suppliers, it should be cooperative because both companies, in some way, work together. One needs the other. When there is an awareness that both benefit from a good relationship, the tendency to cooperate is greater.
Moreover, maintaining a healthy relationship with suppliers can generate an advantage over the competition. The commitment of one to the other is often reflected, for example, in the quality of raw materials and shorter delivery times, which will ensure better products and services to the end consumer.
At this point, it is good to remember that no company functions without interactions.
When looking at relationship management, the company has advantages such as better performance throughout the chain, a broader understanding of values and goals, an increased ability to create even more value, and more effective management of quality-related risks.
To implement this principle, among other actions, it is necessary to establish harmonious relationships.
What is the Impact of the Principles on the Quality Management System?
Now that you know the 7 principles of quality management, you can apply them in your business to ensure improvements in all aspects. The mentioned principles are a way to ensure that your company is prepared to continuously create value for people.
The impact of the 7 principles is enormous, as they are fundamental elements that enable the creation and maintenance of a solid foundation for the implementation and maintenance of a quality management system. Already mentioned, ISO 9001:2015 addresses the benefits of taking the implementation of a quality management system seriously.
The objective of quality principles is to stimulate the effectiveness of processes within an organization, which automatically contributes to its establishment in the market. Therefore, they are nothing more than a strategic and intelligent way to make a company grow and develop. In other words, investing in quality is investing in the longevity of the company.
Perhaps you have already noticed that all the principles are interconnected within the quality management system. The evolution of one promotes the evolution of another and so on.
Therefore, maintaining a focus on the customer is much easier when there is the presence of good leadership. Leaders who inspire promote greater engagement and delivery from the team. With this attitude, processes can be adopted and analyzed correctly.
Then, it is possible to review and gather data, from which processes can be improved. With the practice of these principles, it is easier to create and nurture good relationships, especially with customers. In the end, it is clear that ensuring customer satisfaction happens more naturally, achieving the overarching goal of every company.
If you are considering implementing a management system, make use of the 7 principles of quality management to act and support your decisions, as they are certainly aligned with the success of any business!